What is a Process Challenge Device (PCD) for Sterilization Monitoring?
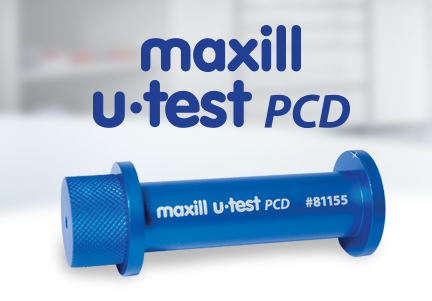
We're proud to introduce the ‘new guy’ in the IPAC line up of products: maxill u-test PCD - Process Challenge Device.
A process challenge device is a key element in the quality assurance testing of dental office sterilizers.
It is used to monitor the performance of the sterilization process.
The process challenge device simulates an equal or greater challenge than the most difficult instrument/item routinely processed in a sterilization cycle.
Each day and each cycle requires the use of a process challenge device.
Adding a more rigorous approach to testing follows best practice within the risk management of the theory of routine practice principles of infection prevention and control.
Process challenge devices are supported for use by regulatory bodies and sterilizer manufacturers.
The history of the process challenge device traces to the longevity of use in Europe for several years as the gold standard to quality assurance.
Depending on the geographical area there may be variations of the mention of use from the dental and public health regulatory bodies.
At this exact moment, process challenge device’s are the hot topic in the province of Ontario.
Nonetheless, other geographical areas will need them based on total ‘best practice’ and directing dental professionals to read the fine print in their sterilizer’s user handbook.
Parts of a Manufactured Process Challenge Device (PCD)
The cap is removed to place a BI and CI inside the hollow body of the process challenge device.
The opposing end to the cap has a small hole to allow the steam to penetrate inside the body of the process challenge device.
A narrow opening makes it a challenge for the steam to enter.
An enclosed capsule makes it difficult for the heat to penetrate, thus offering extra challenges to the testing.
See the image below.
Types of Process Challenge Devices (PCD’s)
The maxill u-test PCD works in conjunction with a biological indicator (BI) and chemical integrator (CI).
To further qualify and challenge the testing the CI and BI need to be placed in a container that mimics the sterilization environment.
Consider this as the quality assurance on the quality assurance.
There are two ways this can be done:
- in-office made process challenge device
- Commercially made process challenge device ( maxill u-test PCD )
Is one better than the other?
Does one work better than the other?
Yes and yes!!
Up until now with the introduction of the maxill u-test process challenge device, there have been no commercially available process challenge device’s in North America.
Dental offices were forced to go with an in-office process challenge device that uses a cassette with metal instruments or a bag with a bunch of metal instruments overpacked in the bag.
A BI and CI type V are strategically placed in the cassette/pouch versus being placed on their own in the sterilizer as in past practice.
This is meant to mimic the environment of a typical kit of instruments and becomes the control.
How Does a Control Variable Work in Science?
When using controls in science the control must have repeatable properties with no variations.
In other words, the control must be the same every single time as good-quality, measurable evidence.
With human error and simply not being able to replicate the exact same properties from one in-office made control to the next, commercially made controls offer the security of a steady scientific test.
The other issue with the in-office is that it takes up space in the sterilizer.
So instead of taking up an entire pack or cassette spot in the sterilizer, the office can use the small commercially prepared process challenge device.
The other note is that the manufacturer of the sterilizer’s state in their guidebook to find the ‘cold spot’.
This is the area in the sterilizer where the steam has difficulty reaching.
In most sterilizers, the cold spot is located in a small, confined area where the commercially prepared PROCESS CHALLENGE DEVICE can be positioned.
The in-office made process challenge device likely cannot be positioned in the exact cold spot, only in the vicinity.
What Does a PCD Simulate?
A process challenge device simulates the most challenging instrument to sterilize and has been designed to hold a maxill Biological Indicator and a Type V Chemical Integrator.
The hollow interior is the reservoir for the BI and CI.
The inside of a process challenge device is designed to, mimic the inside of a dental handpiece.
The maxill u-test PCD was designed to replace the office made process challenge device.
As stated above, it saves space in the sterilizer and makes it easy for anyone in the office to re-create the same sterilization challenge over and over again.
The process challenge device is placed in a sterilization pouch and fits nicely in our steri-sox 3.5 x 9 pouch.
How To Use A Manufactured Process Challenge Device
The process challenge device has two testing properties:
- Daily routine testing of a sterilizer for each selected cycle (an office would need one PCD per sterilizer)
- Qualifying and re-qualifying a sterilizer in the event of any disruption to its regular activities as well as under the following specific circumstances:
- Introduction and installation of a new sterilizer
- Circulation of a ‘loaner’ sterilizer
- Post any environmental changes in the area housing the sterilizer (construction/renovation)
- Relocation of the sterilizer
- Repairs / alterations to the sterilizer
- Sterilization failures
- Any professional judgment that suspects an issue in the function of the sterilizer
The qualifying and re-qualifying steps include 3 BI tests to be performed consecutively in an empty test load with the Type V CI and BI placed in a process challenge device, process and incubate.
Once confirmed that all 3 BI’s as well as chemical and mechanical testing display a ‘pass’ then the sterilizer can move to a 4th challenge in a full test load.
Again, the CI and BI are required to be placed in a process challenge device for the 4th load and with all three (BI, CI and mechanical) meeting testing criteria, the sterilizer can be utilized.
A sterilizer is not fit for use if any quality assurance indicators conclude a failed outcome.
Evaluation of the results of the BI and CI remains the same with the use of a PROCESS CHALLENGE DEVICE.
Continue to follow the BI and CI and your sterilizers MIFU (Manufacturers Instructions for Use), as well as the regulatory bodies frequency of testing.
The use of a process challenge device does not alter the frequency of testing.
Best practice indicates a BI in a process challenge device and control BI are to be tested and logged daily in the morning/first load of the day with routine daily use.
Best practice indicates a CI Type V or VI in a process challenge device is to be tested and logged daily in every cycle type used that day with routine daily use.
Additional Information
How to Use PCD’s Flow Chart (RCDSO):
RCDSO - How to Use Chemical Indicators, Biological Indicators and Process Challenge Devices to Monitor Sterilization
Want More Information?
IPAC Standards. Royal College of Dental Surgeons of Ontario (RCDSO) See Page 24 for PCD’s.
RCDSO Standard of Practice - IPAC
IPAC Guidelines. College of Dental Hygienists of Ontario (CDHO) See Page 29 for PCD’s.
CDHO Infection Prevention and Control (IPAC) Guidelines
What to do when Your Sterilization Quality Assurance Monitoring Fails. Read all pages. College of Dental Hygienists of Ontario (CDHO)
what-to-do-when-your-sterilization-quality-assurance-monitoring-fails.pdf